يُصنع الخشب الرقائقي من ثلاث طبقات رقيقة أو أكثر من الخشب، ملتصقة ببعضها البعض بمادة لاصقة. عادةً ما تكون كل طبقة من الخشب، أو الرقائق، موجهة بحيث تكون أليافها متعامدة مع الطبقة المجاورة، وذلك لتقليل الانكماش وتحسين متانة القطعة النهائية. يُضغط معظم الخشب الرقائقي على شكل صفائح مسطحة كبيرة تُستخدم في البناء. كما يمكن تشكيل قطع أخرى من الخشب الرقائقي على شكل منحنيات بسيطة أو مركبة، لاستخدامها في صناعة الأثاث والقوارب والطائرات.
يعود استخدام طبقات الخشب الرقيقة في البناء إلى حوالي عام ١٥٠٠ قبل الميلاد، عندما قام الحرفيون المصريون بلصق قطع رقيقة من خشب الأبنوس الداكن على الجزء الخارجي من صندوق من خشب الأرز عُثر عليه في مقبرة الملك توت عنخ آمون. استخدم الإغريق والرومان هذه التقنية لاحقًا لإنتاج أثاث فاخر وتحف زخرفية أخرى. في القرن السابع عشر، عُرف فن تزيين الأثاث بقطع خشبية رقيقة باسم "القشرة"، وأصبحت القطع نفسها تُعرف باسم "القشرة".
حتى أواخر القرن الثامن عشر، كانت قطع القشرة تُقطع يدويًا بالكامل. في عام ١٧٩٧، قدّم الإنجليزي السير صموئيل بنثام طلبًا للحصول على براءات اختراع لعدة آلات لإنتاج القشرة. في طلبات براءات الاختراع التي قدّمها، وصف مفهوم تصفيح عدة طبقات من القشرة بالغراء لتشكيل قطعة أكثر سمكًا - وهو أول وصف لما يُسمى الآن بالخشب الرقائقي.
على الرغم من هذا التطور، استغرق الأمر قرابة مئة عام أخرى قبل أن تجد القشرة الخشبية الرقائقية أي استخدامات تجارية خارج صناعة الأثاث. في حوالي عام ١٨٩٠، استُخدمت الأخشاب الرقائقية لأول مرة في صناعة الأبواب. ومع ازدياد الطلب، بدأت عدة شركات بإنتاج صفائح من الخشب الرقائقي متعدد الطبقات، ليس فقط للأبواب، بل أيضًا للاستخدام في عربات السكك الحديدية والحافلات والطائرات. على الرغم من هذا الاستخدام المتزايد، إلا أن مفهوم استخدام "الأخشاب المُلصقة"، كما أطلق عليها بعض الحرفيين ساخرين، قد ولّد صورة سلبية عن المنتج. لمواجهة هذه الصورة، اجتمع مصنعو الأخشاب الرقائقية واستقروا أخيرًا على مصطلح "الخشب الرقائقي" لوصف المادة الجديدة.
في عام ١٩٢٨، طُرحت أول ألواح خشب رقائقي قياسية بأبعاد ١.٢ متر × ٢.٤ متر (٤ أقدام × ٨ أقدام) في الولايات المتحدة الأمريكية لاستخدامها كمواد بناء عامة. وفي العقود التالية، أتاحت المواد اللاصقة المُحسّنة وطرق الإنتاج الجديدة استخدام الخشب الرقائقي في مجموعة واسعة من التطبيقات. واليوم، حل الخشب الرقائقي محل الأخشاب المقطوعة في العديد من أغراض البناء، وأصبحت صناعته صناعة عالمية تُقدر قيمتها بمليارات الدولارات.
تُعرف الطبقات الخارجية من الخشب الرقائقي بالوجه والظهر على التوالي. الوجه هو السطح المراد استخدامه أو رؤيته، بينما يبقى الظهر غير مستخدم أو مخفي. تُعرف الطبقة الوسطى باللب. في الخشب الرقائقي ذي الخمس طبقات أو أكثر، تُعرف الطبقات المتوسطة بالأشرطة المتقاطعة.
يمكن صنع الخشب الرقائقي من الأخشاب الصلبة، أو الأخشاب اللينة، أو مزيج منهما. من بين الأخشاب الصلبة الشائعة خشب الدردار، والقيقب، والماهوجني، والبلوط، والساج. أكثر أنواع الأخشاب اللينة شيوعًا في الولايات المتحدة هو خشب التنوب دوغلاس، مع استخدام أنواع أخرى من الصنوبر، والأرز، والتنوب، والخشب الأحمر.
الخشب الرقائقي المركب له قلب مصنوع من ألواح خشبية مضغوطة أو قطع من الخشب الصلب متصلة ببعضها. يُغطى سطحه وظهره بقشرة من الخشب الرقائقي. يُستخدم الخشب الرقائقي المركب عند الحاجة إلى ألواح سميكة جدًا.
يعتمد نوع اللاصق المستخدم لربط طبقات الخشب معًا على الاستخدام المحدد للخشب الرقائقي النهائي. عادةً ما تستخدم ألواح الخشب الرقائقي اللينة المصممة للتركيب على الأسطح الخارجية للمباني راتنج الفينول فورمالدهيد كمادة لاصقة نظرًا لمتانتها ومقاومتها الممتازة للرطوبة. أما ألواح الخشب الرقائقي اللينة المصممة للتركيب على الأسطح الداخلية للمباني، فقد تستخدم لاصق بروتين الدم أو بروتين فول الصويا، مع أن معظم ألواح الخشب الرقائقي الداخلية مصنوعة الآن من نفس راتنج الفينول فورمالدهيد المستخدم في الألواح الخارجية. أما الخشب الرقائقي الصلب المستخدم في التطبيقات الداخلية وفي صناعة الأثاث، فعادةً ما يُصنع من راتنج اليوريا فورمالدهيد.
تتطلب بعض التطبيقات ألواح خشب رقائقي بطبقة رقيقة من البلاستيك أو المعدن أو الورق أو القماش المشبع بالراتنج، مثبتة إما على الوجه أو الخلف (أو كليهما) لمنح السطح الخارجي مقاومة إضافية للرطوبة والتآكل أو لتحسين قدرته على الاحتفاظ بالطلاء. يُطلق على هذا النوع من الخشب الرقائقي اسم الخشب الرقائقي المتراكب، ويُستخدم عادةً في قطاعات البناء والنقل والزراعة.
يمكن طلاء صفائح الخشب الرقائقي الأخرى بصبغة سائلة لإعطاء الأسطح مظهرًا نهائيًا، أو يمكن معالجتها بمواد كيميائية مختلفة لتحسين مقاومة الخشب الرقائقي للهب أو مقاومته للتسوس.
هناك فئتان عريضتان من الخشب الرقائقي، ولكل منهما نظام تصنيف خاص بها.
تُعرف إحدى فئتي الخشب الرقائقي بالبناء والصناعي. تُستخدم أخشاب الرقائق في هذه الفئة أساسًا لمتانتها، وتُصنف حسب قابليتها للتعرض ودرجة القشرة المستخدمة على السطح والظهر. قد تكون قابلية التعرض داخلية أو خارجية، حسب نوع الغراء. قد تكون درجات القشرة N أو A أو B أو C أو D. تتميز الدرجة N بعيوب سطحية قليلة جدًا، بينما قد تحتوي الدرجة D على العديد من العقد والشقوق. على سبيل المثال، يُصنف الخشب الرقائقي المستخدم في الأرضيات السفلية في المنازل بتصنيف "داخلي CD". هذا يعني أن له وجهًا C وظهرًا D، والغراء مناسب للاستخدام في المواقع المحمية. تُصنع الطبقات الداخلية لجميع أخشاب الرقائقي الإنشائية والصناعية من قشرة من الدرجة C أو D، بغض النظر عن التصنيف.
النوع الآخر من الخشب الرقائقي يُعرف بالخشب الصلب والزخرفي. يُستخدم هذا النوع من الخشب أساسًا لمظهره، ويُصنّف تنازليًا حسب مقاومته للرطوبة إلى: تقني (خارجي)، النوع الأول (خارجي)، النوع الثاني (داخلي)، والنوع الثالث (داخلي). قشرة سطحه خالية تقريبًا من العيوب.
المقاسات
تتراوح سماكة ألواح الخشب الرقائقي بين 1.6 مم (0.6 بوصة) و76 مم (3.0 بوصة). وتتراوح السماكات الأكثر شيوعًا بين 6.4 مم (0.25 بوصة) و19.0 مم (0.75 بوصة). ورغم أن قلب لوح الخشب الرقائقي، وأشرطةه المستعرضة، ووجهه وخلفه قد تكون مصنوعة من قشور بسماكات مختلفة، إلا أن سماكة كل منها يجب أن تكون متوازنة حول المركز. على سبيل المثال، يجب أن يكون سماكة الوجه والخلف متساوية. وبالمثل، يجب أن تكون أشرطةه المستعرضة العلوية والسفلية متساوية.
الحجم الأكثر شيوعًا لألواح الخشب الرقائقي المستخدمة في البناء هو 1.2 متر (4 أقدام) عرضًا و2.4 متر (8 أقدام) طولًا. ومن العروض الشائعة الأخرى 0.9 متر (3 أقدام) و1.5 متر (5 أقدام). وتتراوح الأطوال بين 2.4 متر (8 أقدام) و3.6 متر (12 قدمًا) بزيادات قدرها 0.3 متر (1 قدم). قد تتطلب تطبيقات خاصة، مثل بناء القوارب، ألواحًا أكبر.
الأشجار المستخدمة في صناعة الخشب الرقائقي عادةً ما تكون أصغر قطرًا من تلك المستخدمة في صناعة الأخشاب. في معظم الحالات، تُزرع وتُنمّى في مناطق مملوكة لشركة الخشب الرقائقي. تُدار هذه المناطق بعناية لتعزيز نمو الأشجار وتقليل أضرار الحشرات والحرائق.
فيما يلي تسلسل نموذجي للعمليات الخاصة بمعالجة الأشجار وتحويلها إلى صفائح خشب رقائقي قياسية مقاس 4 أقدام × 8 أقدام (1.2 متر × 2.4 متر):
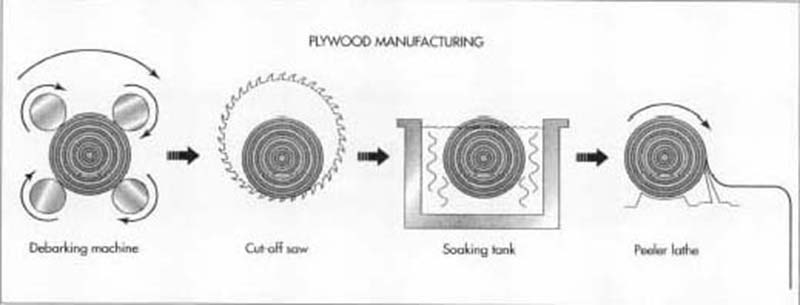
تُنزع قشرتها أولاً، ثم تُقطع إلى قطع قابلة للتقشير. ولقطعها إلى شرائح من القشرة، تُنقع أولاً، ثم تُقشر.
١. تُعَلَّم الأشجار المختارة في منطقة ما بأنها جاهزة للقطع أو الإزالة. يمكن قطع الأشجار باستخدام مناشير تعمل بالبنزين أو بمقصات هيدروليكية كبيرة تُركَّب على مقدمة المركبات ذات العجلات. تُزال الأغصان من الأشجار المتساقطة باستخدام المناشير.
تُسحب جذوع الأشجار المقصوصة، أو جذوع الأشجار، إلى منطقة التحميل بواسطة مركبات ذات عجلات تُسمى الجرافات. تُقطع الجذوع حسب الطول المطلوب، وتُحمّل على شاحنات لنقلها إلى مصنع الخشب الرقائقي، حيث تُكدّس في أكوام طويلة تُعرف باسم أسطح جذوع الأشجار.
عند الحاجة إلى جذوع الأشجار، تُجمع من أسطحها بواسطة رافعات ذات إطارات مطاطية، وتُوضع على ناقل تسلسلي ينقلها إلى آلة نزع اللحاء. تزيل هذه الآلة اللحاء، إما بعجلات طحن حادة الأسنان أو بنفثات ماء عالية الضغط، بينما تدور الجذع ببطء حول محورها الطويل.
تُنقل جذوع الأشجار المُنزوعة اللحاء إلى المصنع على ناقل سلسلة، حيث يقطعها منشار دائري ضخم إلى أقسام يتراوح طولها بين 2.5 متر و2.6 متر، مناسبة لصنع صفائح قياسية بطول 2.4 متر. تُعرف هذه الأقسام باسم كتل التقشير.
قبل قطع القشرة، يجب تسخين كتل التقشير ونقعها لتليين الخشب. يمكن تبخير الكتل أو غمرها في الماء الساخن. تستغرق هذه العملية من ١٢ إلى ٤٠ ساعة، حسب نوع الخشب وقطر الكتلة وعوامل أخرى.
٦ تُنقل بعد ذلك كتل التقشير المُسخّنة إلى مخرطة التقشير، حيث تُحاذى وتُغذّى تلقائيًا واحدة تلو الأخرى. أثناء دوران المخرطة للكتلة بسرعة حول محورها الطويل، تقوم شفرة سكين كاملة الطول بتقشير طبقة متصلة من القشرة من سطح الكتلة الدوارة بمعدل ٣٠٠-٨٠٠ قدم/دقيقة (٩٠-٢٤٠ مترًا/دقيقة). عندما يُقلّص قطر الكتلة إلى حوالي ٢٣٠-٣٠٥ مم (٣-٤ بوصات)، تُطرد قطعة الخشب المتبقية، المعروفة باسم لبّ التقشير، من المخرطة وتُغذّى كتلة تقشير جديدة في مكانها.
يمكن معالجة صفيحة القشرة الطويلة الخارجة من مخرطة التقشير فورًا، أو تخزينها في صواني طويلة متعددة المستويات، أو لفّها على بكرات. على أي حال، تتضمن العملية التالية تقطيع القشرة إلى عرض قابل للاستخدام، عادةً حوالي 1.4 متر (4 أقدام - 6 بوصات)، لصنع صفائح خشب رقائقي قياسية بعرض 1.2 متر (4 أقدام). في الوقت نفسه، تبحث الماسحات الضوئية عن المقاطع ذات العيوب غير المقبولة، وتُقصّ هذه المقاطع، تاركةً قطع قشرة بعرض أقل من العرض القياسي.
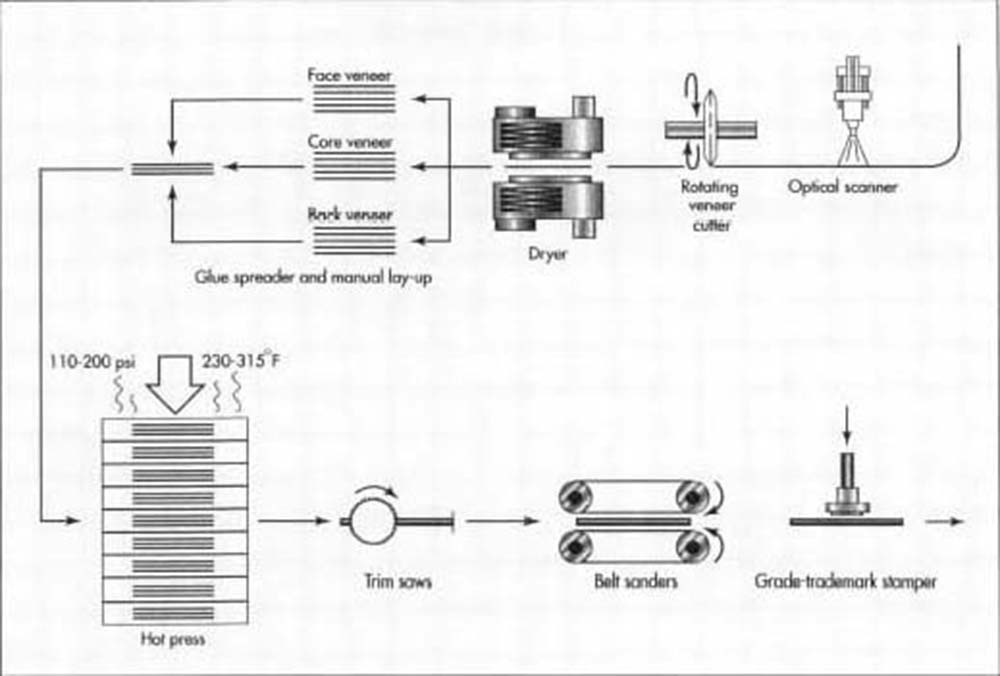
تُلف شرائح القشرة الرطبة على شكل لفافة، بينما يكتشف ماسح ضوئي أي عيوب غير مقبولة في الخشب. بعد جفافها، تُصنف القشرة وتُرص. تُلصق أجزاء مختارة من القشرة معًا. تُستخدم مكبس ساخن لإغلاق القشرة في قطعة واحدة صلبة من الخشب الرقائقي، والتي تُقص وتُصنفر قبل ختمها بالدرجة المناسبة.
تُفرز بعد ذلك أقسام القشرة وتُرص حسب الدرجة. يمكن القيام بذلك يدويًا أو آليًا باستخدام الماسحات الضوئية.
تُغذّى الأجزاء المُفرزة في مجفف لتقليل رطوبتها والسماح لها بالانكماش قبل لصقها. تستخدم معظم مصانع الخشب الرقائقي مجففًا ميكانيكيًا تتحرك فيه القطع باستمرار عبر حجرة مُسخّنة. في بعض المجففات، تُنفث نفثات هواء ساخن عالي السرعة على سطح القطع لتسريع عملية التجفيف.
عند خروج أجزاء القشرة من المجفف، تُرص حسب درجة الجودة. تُلصق أجزاء القشرة الإضافية على الأجزاء السفلية بشريط لاصق أو غراء لجعل القطع مناسبة للاستخدام في الطبقات الداخلية حيث يكون المظهر والمتانة أقل أهمية.
11 يتم قطع أقسام القشرة التي سيتم تركيبها بشكل عرضي - اللب في صفائح ثلاثية الطبقات، أو الأشرطة العرضية في صفائح خماسية الطبقات - إلى أطوال تبلغ حوالي 4 أقدام و3 بوصات (1.3 متر).
١٢- عند تجميع أجزاء القشرة المناسبة لطبقة معينة من الخشب الرقائقي، تبدأ عملية رصّ القطع ولصقها معًا. يمكن القيام بذلك يدويًا أو شبه آليًا باستخدام الآلات. في أبسط حالات الألواح ثلاثية الطبقات، تُفرد القشرة الخلفية وتُمرّر عبر ناشر الغراء، الذي يضع طبقة من الغراء على السطح العلوي. ثم تُوضع الأجزاء القصيرة من القشرة الأساسية بشكل عرضي فوق القشرة الخلفية الملصقة، وتُمرّر الصفيحة بأكملها عبر ناشر الغراء مرة أخرى. وأخيرًا، تُوضع القشرة الأمامية فوق الطبقة الأساسية الملصقة، وتُرصّ الصفيحة مع صفائح أخرى تنتظر دخولها إلى المكبس.
تُحمَّل الألواح المُلصقة في مكبس ساخن متعدد الفتحات. يُمكن للمكابس التعامل مع ٢٠-٤٠ ورقة في المرة الواحدة، مع تحميل كل ورقة في فتحة منفصلة. بعد تحميل جميع الألواح، يقوم المكبس بضغطها معًا تحت ضغط يتراوح بين ١١٠-٢٠٠ رطل/بوصة مربعة (٧.٦-١٣.٨ بار)، مع تسخينها في الوقت نفسه إلى درجة حرارة تتراوح بين ١٠٩.٩-١٥٧.٢ درجة مئوية (٢٣٠-٣١٥ درجة فهرنهايت). يضمن الضغط التلامس الجيد بين طبقات القشرة، وتُساعد الحرارة على تصلب الغراء بشكل صحيح لتحقيق أقصى قوة. بعد فترة تتراوح بين ٢ و٧ دقائق، يُفتح المكبس وتُفرَّغ الألواح.
تُمرَّر الألواح الخشنة بعد ذلك عبر مجموعة من المناشير، لتشذيبها وصولاً إلى عرضها وطولها النهائيين. تُمرَّر الألواح عالية الجودة عبر مجموعة من صنفرة الحزام بعرض 1.2 متر (4 أقدام)، لصنفرة السطح والظهر. تُصنَّر الألواح متوسطة الجودة يدويًا لتنظيف المناطق الخشنة. تُمرَّر بعض الألواح عبر مجموعة من شفرات المنشار الدائري، التي تُحدِث أخاديد سطحية في السطح لإضفاء مظهر مُحكم على الخشب الرقائقي. بعد الفحص النهائي، تُصلَح أي عيوب متبقية.
تُختم الأوراق النهائية بعلامة تجارية تُعطي المشتري معلومات عن درجة التعرض، والدرجة، ورقم المصنع، وعوامل أخرى. تُربط الأوراق التي تحمل العلامة التجارية نفسها معًا في أكوام، وتُنقل إلى المستودع لانتظار الشحن.
كما هو الحال مع الأخشاب، لا وجود لقطعة خشب رقائقي مثالية. جميع قطع الخشب الرقائقي بها عدد معين من العيوب. يحدد عدد هذه العيوب وموقعها درجة جودة الخشب الرقائقي. تُحدد معايير الخشب الرقائقي الإنشائي والصناعي من خلال معيار المنتج PS1 الذي أعده المكتب الوطني للمعايير والجمعية الأمريكية للخشب الرقائقي. أما معايير الخشب الصلب والخشب الرقائقي الزخرفي فتُحدد من خلال معيار ANSIIHPMA HP الذي أعده المعهد الوطني الأمريكي للمعايير والجمعية الأمريكية لمصنعي الخشب الرقائقي. لا تقتصر هذه المعايير على تحديد أنظمة تصنيف الخشب الرقائقي فحسب، بل تحدد أيضًا معايير البناء والأداء والاستخدام.
على الرغم من أن الخشب الرقائقي يستخدم الأشجار بكفاءة عالية - إذ يُفككها ويعيد تركيبها في هيكل أقوى وأكثر قابلية للاستخدام - إلا أن عملية التصنيع تنطوي على هدر كبير. في معظم الحالات، لا يُحوّل إلى خشب رقائقي سوى ما يقارب 50-75% من حجم الخشب الصالح للاستخدام في الشجرة. ولتحسين هذه النسبة، يجري تطوير العديد من المنتجات الجديدة.
أحد المنتجات الجديدة هو لوح الخيوط الموجهة، الذي يُصنع بتقطيع جذع الشجرة بالكامل إلى خيوط، بدلاً من تقشير القشرة والتخلص من اللب. تُخلط الخيوط بمادة لاصقة وتُضغط في طبقات بحيث يكون اتجاه العروق في اتجاه واحد. ثم تُوجه هذه الطبقات المضغوطة بزوايا قائمة على بعضها البعض، مثل الخشب الرقائقي، وتُلصق ببعضها. يتميز لوح الخيوط الموجهة بمتانة الخشب الرقائقي وسعره الأقل قليلاً.
وقت النشر: ١٠ أغسطس ٢٠٢١